INFORMATION
Address: 107 Deligiorgi Str., Bld of Industrial Management & Technology, 1st floor
MEMBERS
Director
Laboratory Teaching Staff
DESCRIPTION
The Laboratory of Production Management Information Systems (PMIS) provides students with the necessary IT equipment and software for their studies. Moreover, it enables teaching and research in the areas of design and development of IT applications (multimedia, Internet, Databases), simulation of production and distribution systems, and ergonomics.
COURSES SUPPORTED BY THE LABORATORY
Undergraduate courses
- Introduction to Computers (1st sem.)
- e-Business – Multimedia (2nd sem.)
- Statistics (3rd sem.)
- Operations Research I (4th sem.)
- Data Processing & Programming Languages (4th sem.)
- Production System Design (4th sem.)
- Operations Research II (5th sem.)
- Information Systems (5th sem.)
- Production Planning & Control (5th sem.)
- Queueing Theory & System Simulation (6th sem.)
- Project Management (6th sem.)
- Artificial Intelligence (7th sem. elective)
Postgraduate courses
-
Analytical Methods
-
Project Management
-
Project Management Information Systems
-
Quality & Risk Management
-
ERP Systems in the Supply Chain – Applications with SAP
-
Advanced Topics in ERP Systems – Applications with SAP
-
ERP Systems in Project Management & Product Development – Applications with SAP
RESEARCH PROJECTS
Energy-aware Factory Analytics for Process Industries (FACTLOG)
2019 – 2023
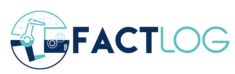
FACTLOG will develop a system that applies the innovative concept of the Enhanced Cognitive Twin. The digital twin technology uses a digital (virtual) model of a real (industrial or other) system (i.e. resources, processes, people, locations, systems, equipment and devices, even software and procedures) enabling monitoring the system, simulating its behaviour. The cognitive digital twin is the evolution of the digital twin concept in the big data era. It provides cognitive capabilities to the digital twin, enabling learning from the vast streams of data that flow through it and thus the continuous modelling of the physical element’s behaviour. FACTLOG takes this concept a step further with ECT by incorporating an analytical toolkit, enhancing its reasoning capabilities with optimization, big data analytics and simulation tools. This constitutes the ECT not only a valuable tool for monitoring and control but also an indispensable part of the decision-making process that optimizes the operation of the actual system. The applicability of the FACTLOG approach will be demonstrated and evaluated in 4 different application areas, namely oil refineries, textile industry, automotive industry, and steel manufacturing. For more info, please refer here.
Modular Manufacturing and Distributed Control via Interoperable Digital Twins (MODAPTO)
2023-2025
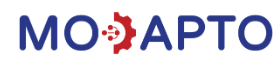
MODAPTO envisions flexible industrial systems composed of modules enhanced by distributed intelligence via interoperable Digital Twins (DTs) based on industrial standards. Moreover, it materializes enables collective intelligence within modular production schemes for effective module and production line design, reconfiguration and decision support. MODAPTO focuses on two technological pillars: (1) Distributed Intelligence & Control via Interoperable Digital Twins and (2) Modular Production Framework & Toolkit. Within MODAPTO, each production module is augmented by a DT offering additional distributed intelligence functionalities. MODAPTO standardizes the module’s interface via AAS to enable coordination with other modules and systems. MODAPTO also proposes a framework for production design and reconfiguration supported by collective intelligence tools. MODAPTO will be implemented in 3 industrial pilots involving 4 manufacturers at 3 different levels to showcase its versatility and applicability. Pilot1 targets the development of production modules (robotic arms) with novel optimization and sustainability capabilities, while Pilot 2 production reconfiguration and optimization even for single lots in in gearmotor assembly. Pilot 3 targets the cooperation of two supply chain collaborators with the use of smart new modules, namely semi-finished product kits and the corresponding smart kit holder, for optimizing the picking process in the automotive industry via mobile robots and optimizing collaboration between these two industries via monitoring the lifecycle of the corresponding kits.